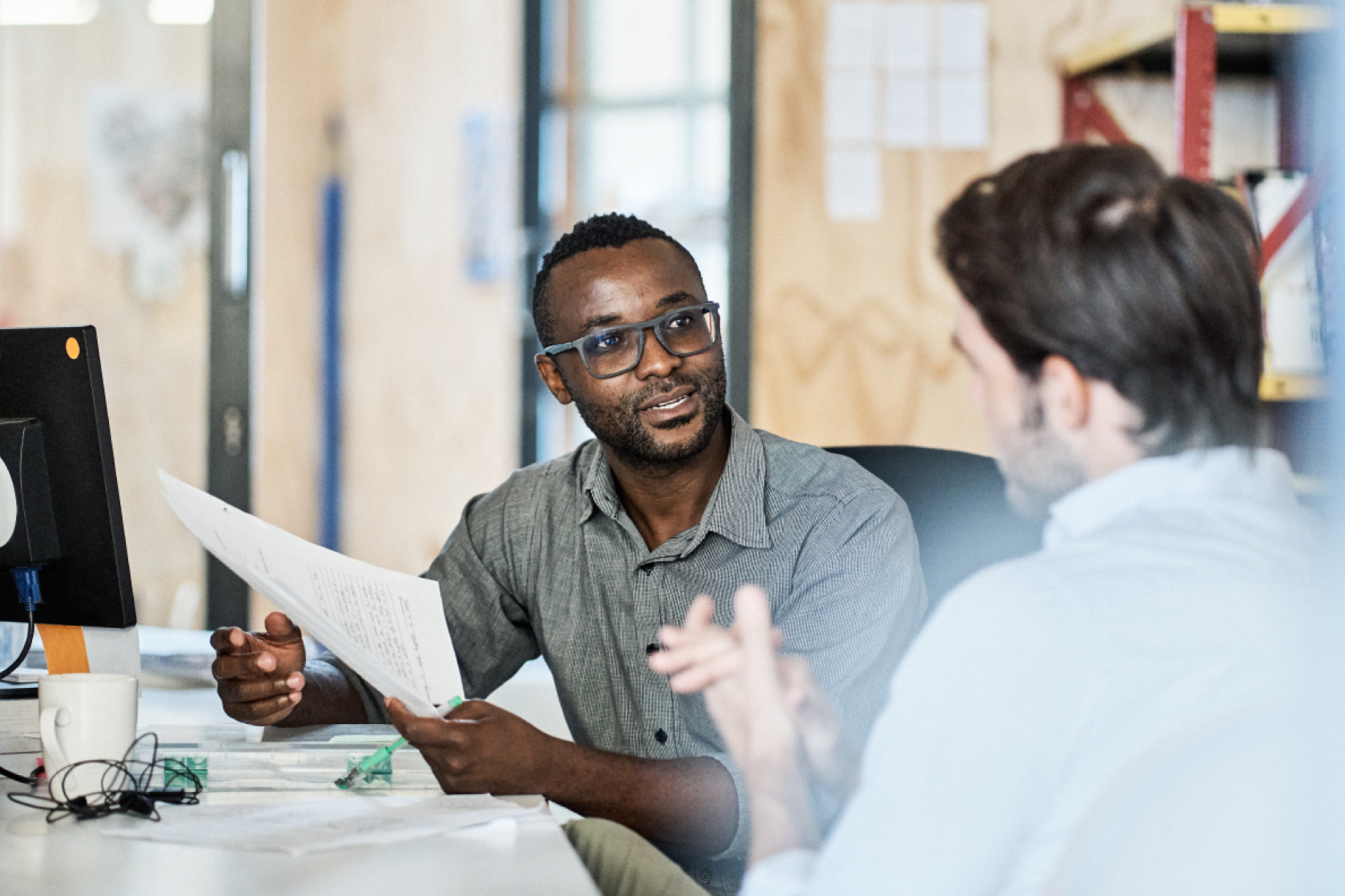
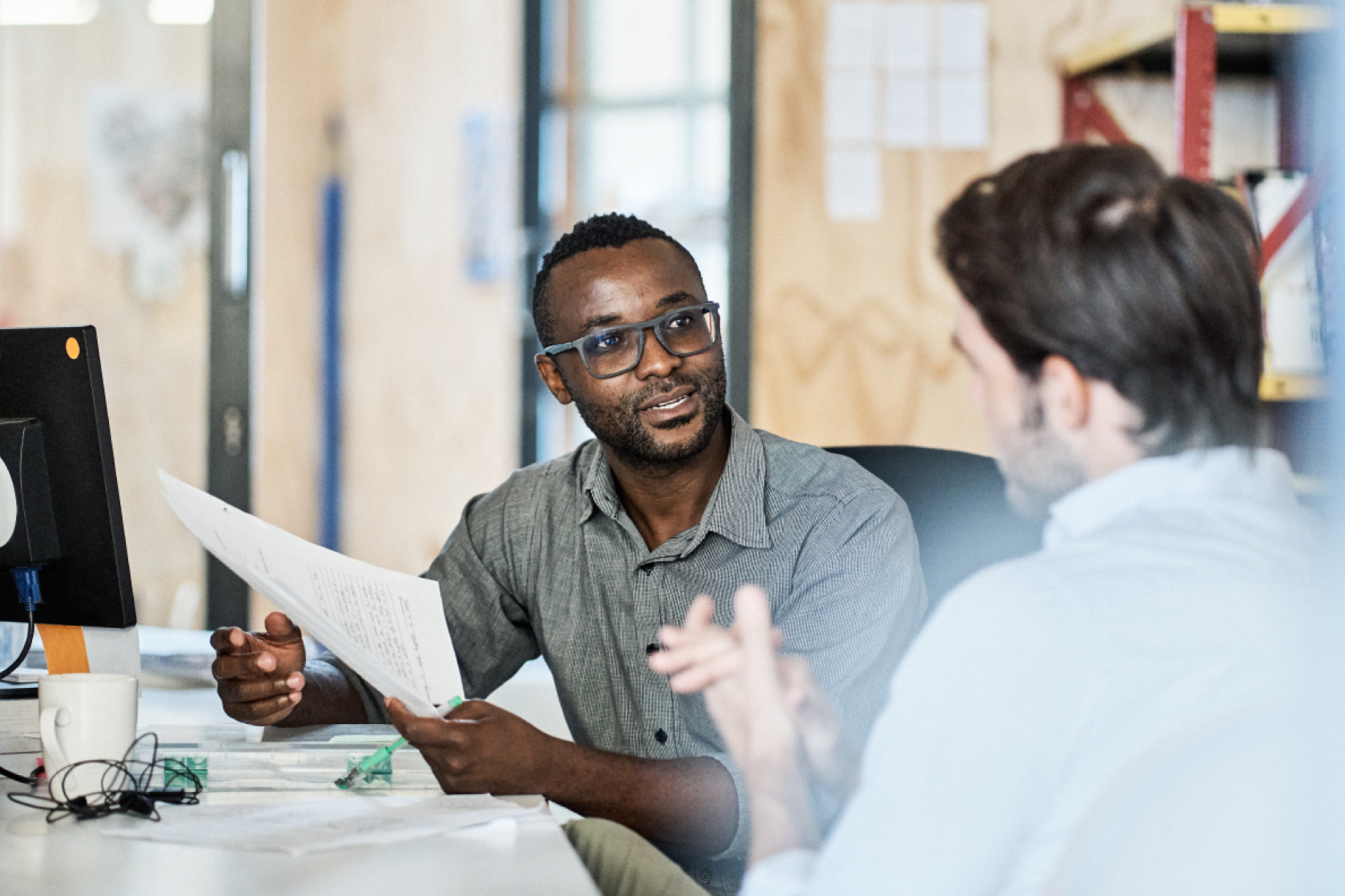
By Amir Bar-Niv, VP of Marketing, Automotive Business Unit, Marvell
Automotive Transformation
Smart Car and Data Center-on-wheels are just some of the terms being used to define the exciting new waves of technology transforming the automotive industry and promising safer, greener self-driving cars and enhanced user experiences. Underpinning it all is a megatrend towards Software-defined Vehicles (SDV). SDV is not just a new automotive technology platform. It also enables a new business model for automotive OEMs. With a software-centric architecture, car makers will have an innovation platform to generate unprecedented streams of revenue from aftermarket services and new applications. For owners, the capability to receive over-the-air software updates for vehicles already on the road – as easily as smartphones are updated – means an automobile whose utility will no longer decline over time and driving experiences that can be continuously improved over time.
This blog is the first in a series of blogs that will discuss the basic components of a system that will enable the future of SDV.
Road to SDV is Paved with Ethernet
A key technology to enable SDVs is a computing platform that is supported by an Ethernet-based In-Vehicle network (IVN). An Ethernet-based IVN provides the ability to reshape the traffic between every system in the car to help meet the requirements of new downloaded applications. To gain the full potential of Ethernet-based IVNs, the nodes within the car will need to “talk” Ethernet. This includes devices such as car sensors and cameras. In this blog, we discuss the characteristics and main components that will drive the creation of this advanced Ethernet-based IVN, which will enable this new era of SDV.
But first let’s talk about the promises of this new business model. For example, people might ask, “how many new applications can possibly be created for cars and who will use them?” This is probably the same question that was asked when Apple created the original AppStore, which started with dozens of new apps, and now of course, the rest is history. We can definitely learn from this model. Plus, this is not going to be just an OEM play. Once SDV cars are on the road, we should expect the emergence of new companies that will develop for the OEMs a whole new world of car applications that will be aligned with other megatrends like Smart City, Mobility as a Service (MaaS), Ride-hailing and many others.
A New Era of Automotive Innovation
Let us now fast forward to the years 2025 to 2030 (which in the automotive industry is considered ‘just around the corner.’) New cars that are designed to support higher level of driver assist systems (ADAS) include anywhere between 20 to 30 sensors (camera, radar, lidar and others). Let’s imagine two new potential applications that could utilize these sensors:
Application 1: “Catch the Car Scratcher” - How many times have we heard of, or even been in, this situation? Someone scratches your car in the parking lot or maliciously scratches your car with a car key. What if the car was able to capture the face of the person or license plate number of the car that caused the damage? Wouldn’t that be a cool feature an OEM could provide to the car owner on demand? If priced right, it most likely could become a popular application. The application could use the accelerometers, and potentially a microphone, to detect the noise of scratching, bumping or hitting the car. Once the car identifies the scratching or bumping, it would activate all of the cameras around the car. The car would then record the video streams into a central storage. This video could later be used by the owner as necessary to recover repair costs through insurance or the courts.
Application 2: “Break-in Attempt Recording” - In this next application, when the system detects a break-in attempt, all internal and external cameras record the video into central storage and immediately upload it to the cloud. This is done in case the car thief tries to tamper with the storage later. In parallel, the user gets a warning signal or alert by phone so they can watch the video streams or even connect to the sound system in the car and scare the thief with their own voice.
We will examine these scenarios more comprehensively in a follow up blog, but these are just two simple examples of the many possible high-value automotive apps that an Ethernet-based IVN can enable in the software-defined car of the future.
Software-Defined Network
Ethernet network standards comprise a long list of features and solutions that have been developed over the years to address real network needs, including the mitigation of security threats. Ethernet was initially adopted by the automotive industry in 2014 and it has since become the dominant network in the car. Once the car’s processors, sensors, cameras and other devices are connected to each other via Ethernet (Ethernet End-to-End), we can realize the biggest promise of SDV: the capability to reprogram the in-vehicle network and adapt its main characteristics to new advanced applications. This capability is called In-Vehicle Software-Defined Networking, or in short, In-vehicle SDN.
Figure 1 shows the building blocks for In-Vehicle SDN that enable SDV.
Figure 1 – Ethernet and SDN as building blocks for SDV
Ethernet features enable four key attributes that are key for SDV: Flexibility, Scalability, Redundancy and Controllability.
In-vehicle SDN is the mechanism that provide the ability to modify and adapt these attributes in SDV. SDN is a technology that uses application programming interfaces (APIs) to communicate with underlying hardware infrastructure, like switches and bridges, and provisions traffic flow in a network. The In-Vehicle SDN allows the separation of control and data planes and brings network programmability to the realm of advanced data forwarding mechanisms in automotive networks.
Cameras and the Ethernet Edge
To realize the full capability of in-vehicle SDN, most devices in the car will need to be connected via Ethernet. In today’s advanced car architectures, the backbone of the high-speed links is all Ethernet. However, camera interfaces are still based on old proprietary point-to-point Low-Voltage Differential Signaling (LVDS) technology. Newer technologies (like MIPI’s A-PHY and ASA) are under development to replace LVDS, but these are still point-to-point solutions. In this blog we refer to all of these solutions as P2PP (Point-to-Point Protocol). In Figure 2, we show an example of a typical zonal car network with the focus on two domains that use the camera sensors: ADAS and Infotainment.
Figure 2 – Zonal network architecture with point-to-point camera links
While most of the ECUs / Sensors / Devices are connected through (and leverage the benefits of) the zonal backbone, cameras are still connected directly (point-to-point) to the processors. Cameras cannot be shared in a simple manner between the two domains (ADAS and IVI), that in many cases are in separate boxes. There is no scalability in this rigid connectivity. Redundancy is also very limited, since the cameras are connected directly to a processor, and any malfunction in this processor might result in lost connection to the cameras.
One potential “solution” for this is to connect the cameras to the zonal switches via P2PP, as shown in Figure 3.
Figure 3 – Zonal network architecture with point-to-point camera links to Zonal switch
This proposal solves only a few of the problems mentioned above but comes at a high cost. To support this configuration the system always needs a dedicated Demux chip, as showed in Figure 4, that converts the P2PP back to camera interface. In addition, to support this configuration, the Zonal switches need a dedicated video interface, like MIPI D-PHY. This interface requires 12 pins per camera (4 pairs for data, 1 pair for clock and 1 pair for control (I2C or SPI)). This adds complexity and many dedicated pins which increases system cost. Another option is to use an external Demux-switch (on top of the Zonal switch) to aggregate multiple P2PP lanes, which is expensive.
Integration of any of these protocols into the Zonal switch is also highly unlikely, since it requires dedicated, non-Ethernet ports on the switch. In addition, no one will consider integration of proprietary or new and non-matured technologies into switches or SoCs.
Figure 4 – Camera P2PP Bridge in Zonal Architecture
Next is controllability, diagnostics and real-time debugging that do not work over the P2PP links in the same simple and standard way they work over Ethernet. This limits the leverage of existing Ethernet-based SW utilities that are used to access, monitor and debug all Ethernet-based ECUs, devices and sensors in the vehicle.
Ethernet Camera Bridge
The right solution for all of these issues is to convert the camera-video to Ethernet – at the edge. A simple bridge device that connects to the camera module and encapsulates the video over Ethernet packets is all it takes, as shown in Figure 5.
Figure 5 – Ethernet Camera Bridge in Zonal Architecture
Since the in-vehicle Ethernet network is Layer 2 (L2)-based, the encapsulation of camera video over Ethernet requires a simple, hard-coded (meaning no SW) MAC block in the bridge device. Figure 6 shows a network that utilizes such bridge devices.
Figure 6 – Zonal architecture with Ethernet End-to-End
The biggest advantage of the Ethernet camera bridge is that it leverages the robustness and maturity of the Ethernet standard. For the Ethernet bridge PHY it means a proven technology (2.5G/5G/10GBASE-T1 and soon 25GBASE-T1) with a very strong ecosystem of cables, connectors, and test facilities (compliance, interoperability, EMC, etc.) that have been accepted by the automotive industry for many years.
But this is only the tip of the iceberg. Once the underlying technology for the camera interface is Ethernet, these links automatically gain access to all the other IEEE Ethernet standards, like:
These important features for automotive networks are covered in a previous Marvell blog called, “Ethernet Advanced Features for Automotive Applications.”
The Ethernet End-to-End with Ethernet camera bridges supports all four key attributes (described in Figure 1) that are required for reliable software-defined car operation: Cameras can easily be shared among domains. Software and hardware can be easily modified independently and scaled all the way up to the camera and sensors. No special video interfaces are needed in the zonal switch – the camera Ethernet link is connected to a standard Ethernet port on the switch, and can be routed on multiple paths, for redundancy. This approach offers the full support of controllability, diagnostic and real-time debugging of the camera links using standard Ethernet utilities that are used in the rest of the in-vehicle network.
So, what’s next? As camera resolutions and refresh rates increase, camera links will need to support future data rates that climb beyond 10Gbps. To support this trend, the IEEE P802.3cy Greater than 10 Gb/s Electrical Automotive Ethernet PHY Task Force is already in the process of defining a standard for 25Gbps automotive PHY. Therefore, we can expect the vehicle backbone as well as Camera Ethernet bridges of up to 25Gbps to be inevitable in the future, and with them, a plethora of even more compelling smart car apps.
Marvell Product Roadmap for Automotive
To help support these new initiatives in automotive technology application and design, Marvell announced the industry’s first multi-gig Ethernet camera bridge solution.
As shown by these announcements, Marvell continues to drive innovation in networking and compute solutions for automotive applications. The Marvell automotive roadmap includes managed Ethernet switches that support the Trusted Boot® feature to enable over-the-air upload of new system configurations, to enable new applications. Marvell custom compute products for automotive are designed in advanced process nodes and leverage Marvell’s IP portfolio of high-performance multi-core processors, end-to-end security and high-speed PHY and SerDes technologies.
To learn more about how Marvell is committed to enabling smarter, safer and greener vehicles with its innovative, end-to-end portfolio of Brightlane™ automotive solutions, check out: https://www.marvell.com/products/automotive.html.
The next blogs in this series will discuss some of the characteristics of SDN-on-wheels, central compute in future vehicles, security structure for vehicle-to-cloud connectivity, in-vehicle-network for infotainment and other exciting developments that enable the future of software-defined vehicle.
By Amir Bar-Niv, VP of Marketing, Automotive Business Unit, Marvell
Ethernet standards comprise a long list of features and solutions that have been developed over the years to resolve real network needs as well as resolve security threats. Now, developers of Ethernet In-Vehicle-Networks (IVN) can easily balance between functionality and cost by choosing the specific features they would like to have in their car’s network.
The roots of Ethernet technology began in 1973, when Bob Metcalfe, a researcher at Xerox Research Center (who later founded 3COM), wrote a memo entitled “Alto Ethernet,” which described how to connect computers over short-distance copper cable. With the explosion of PC-based Local Area Networks (LAN) in businesses and corporations in the 1980s, the growth of client/server LAN architectures continued, and Ethernet started to become the connectivity technology of choice for these networks. However, the Ethernet advancement that made it the most successful networking technology ever was when standardization efforts began for it under the IEEE 802.3 group.